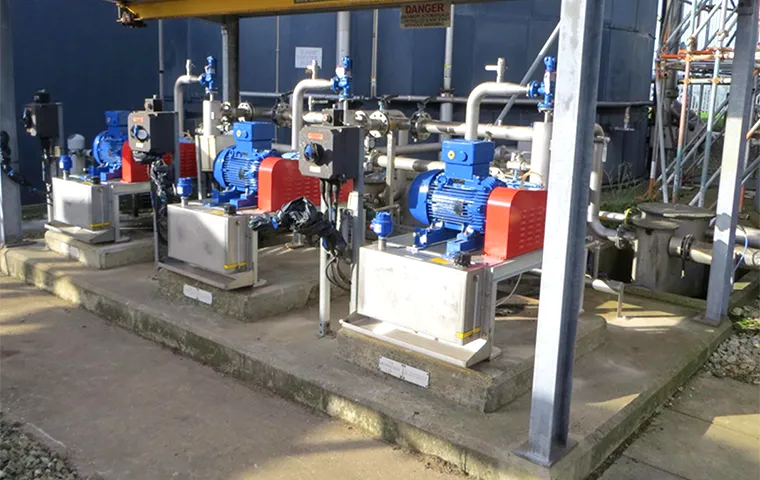
This was the Treatment process plant at Banbury before it was updated
Thames Water – Banbury STW is currently being upgraded both mechanically and electrically.
The project involved the installation of a new CHP (combined heat and power) unit, that will enable the boilers and generators that form part of treatment process, to be supplied with biogas, formed by the anaerobic digestion of waste, which is pumped into the sewage treatment works from the localised catchment area.
The main contractor started these works back in October 2022, but were held up in December, due to the condition of both the gas booster and compressors, where numerous non -conformities from a DSEAR perspective were identified on all the associated electrical and instrumentation equipment.
The main contractor deemed these defects as a risk to their personnel entering the digester area, where further project works were required.
Thames Water were to be counter charged by the main contractor for lost time due to the outstanding DSEAR defects required to comply with BS 60079-14:2014.
These defects had been outstanding since 2015, therefore a quick solution was required.
In consultation with C&P Engineering, Thames Water arranged for all the non-conformity defects to be rectified as soon as practically possible.
C&P attended site and provided a quotation for repairs the next day. C&P reached out to various suppliers of ATEX certified equipment to obtain shorter lead times for the replacement equipment required, as the norm was around eight weeks.
We managed to find a manufacturer through our links to shorten the lead time to 6 weeks. We also arranged a site visit for Thames Water to witness the factory acceptance test. The defective equipment consisted of an Ex d isolator for both the compressor and booster motors and an early break circuit in the way of an emergency stop button, which had been modified into the isolator which is a major Non-Compliance issue with regard BS 60079-14:2014.
There was also a requirement for a heater circuit for each motor.
C&P liaised with the supplier and advised on the design requirements for each isolator, to which an Ex d isolator was designed with the emergency stop button built in, along with additional terminals for the early break and heater circuits required.
All the Intrinsically Safe circuits related to the boosters and compressors were retained, but C&P replaced/rectified the cable containment, along with the circuit cables and glands.
All IS junction boxes were replaced, and a full handover package was provided with the relevant Initial Inspection Documentation to BS 60079-14:2014 and BS 7671 contained within, including all IS loop drawings and specific DSDs
All redundant equipment was either removed or made safe within certified enclosures.
All this was started and completed with ten weeks from inception to completion, inclusive of the material lead times.
Graham Joyce Qualifying Supervisor (DSEAR) Thames Water has passed on his thanks to the C&P DSEAR Engineering Team – September 2023
‘I cannot speak highly enough of C&P Engineering with their efforts in getting these works over the line. They are one of the best companies I have had the pleasure of working with regarding a DSEAR perspective, from back office design, installation and workmanship.’